DISCOVER
Kani shawl
weaving process
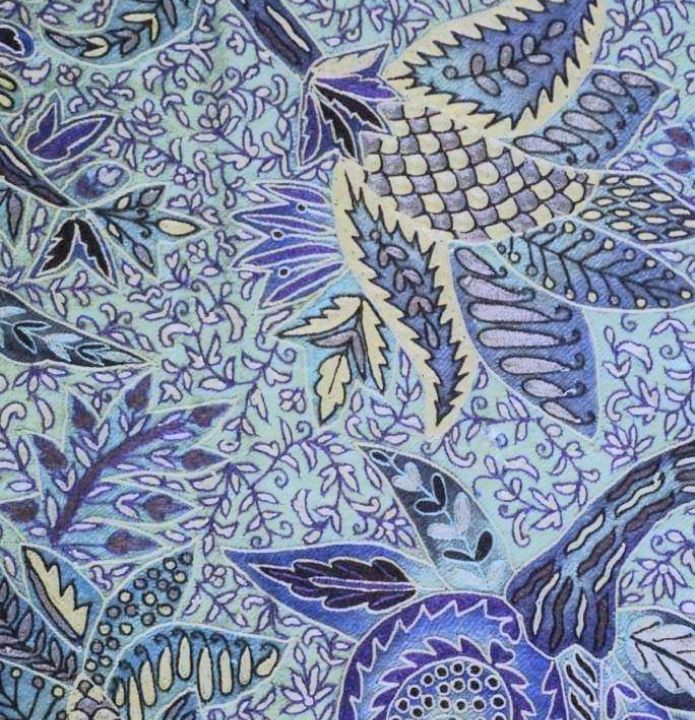
Kani scarves are still woven today
Kani scarves are still woven today, as they were many centuries ago.
The first step to making a Kani scarf is to make the scarf design. The design is hand-drawn on paper from the patterned drawer. After this step, a person known as a dye fills in the colors and calculates the amount of yarn that needs to be dyed. The yarn is sent for dyeing.
Meanwhile, the Designer reproduces the design on graph paper, giving it a geometric look. This replicated design is then placed on the paper below the specified base. This helps to estimate the number of warp threads that each weft has to go through to present the design of the scarf.
Once the warp is laid and the yarns are dyed in different colors and are wound on the jug sticks, the weaver begins the weaving process. Looking at the design of the graph paper and calculating the number of bases through which the inviting stick must pass, the weaver continues to weave the scarf. It takes at least 6-9 months.
Are Kani scarves and ordinary Pashmina scarves woven in the same way?
The most common weave used for cashmere weaving is the twill technique. This technique has many variants, forming diagonal lines or fish bones or the most beautiful, “Kashmir-e-Bulbul”. Kashmir-e-Bulbul forms small diamond-shaped boxes on a scarf and is better known as a diamond weave. “Kashmir-e-Bulbul” means the eye of the bird Bulbul.
Although twill is easier to weave, the diamond weave is more popular for ordinary Pashmina scarves. It adds grace and beauty to Pashmina’s simple scarf.
The looms used to weave Kani scarves and ordinary Pashmina scarves are the same. The only difference is the presence of seamless shuttles with colored yarn wrapped around them for Kani’s scarves. Weavers use a boat-shaped shuttle to weave ordinary scarves. This shuttle is hollow in the middle and has a rod wrapped around it. There is also a small hole or “eye” through which a yarn comes out. This shuttle moves back and forth across the width of the scarf.
For Kani scarves, however, the pre-dyed yarn is wrapped on a small stick called a kani.
The jug sticks are then used to shape the structure as well as the colorful design of the Pashmina scarf.
While a regular scarf will use only one shuttle per weft, a pitcher scarf can have multiple shuttles. The number of stick jugs per weft varies depending on the design that will be created on the scarf. The more complex the design, the greater the number of jug sticks and the longer it takes to weave the scarf.
An average scarf can be woven in three working days; covering about 26-28 inches per day. While, the Kani scarf will progress slowly, taking only about 1/4 of an inch a day. The work done per day depends on the complexity of the design.
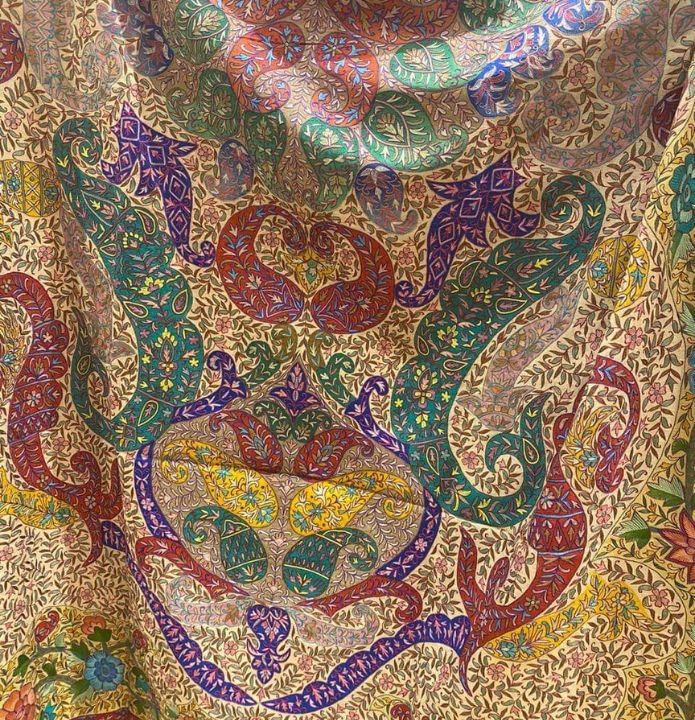
Why is the Kani scarf more expensive than the ordinary Pashmina scarf?
Kani’s scarf, although woven on the same loom as a regular Pashmina scarf, will always be much more expensive. The reason for this is that the design is woven into the fabric, using a centuries-old technique in a very difficult and demanding process.
The production of the Kani scarf by the craftsman takes more than six months to complete, as the design and structure are formed weft by weft along the entire length of the scarf.